
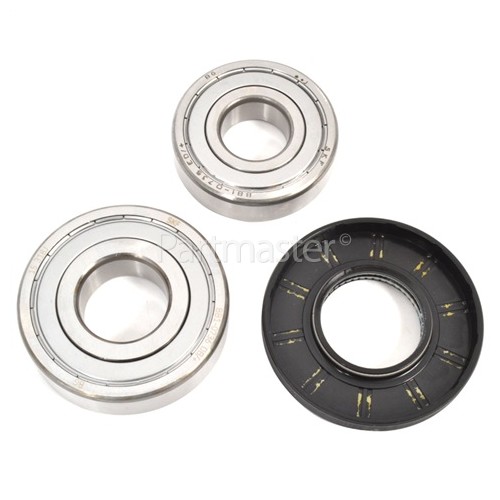
The process engineer is often required to design separators or knockout drums for removing liquids from process gas streams. Kayode Coker, in Ludwig's Applied Process Design for Chemical and Petrochemical Plants (Fourth Edition), VolGAS–LIQUID SEPARATORS The overflow chamber can be designed to flow back automatically into the sealing chamber once the gas velocity decreases below the rate required for closing off the second stage.Ī. It is also common to design the deep seal drum with a concentric overflow chamber to collect the displaced sealing fluid. It is important to design the deep seal drum with a proper gas velocity at the staging point to ensure that all the sealing fluid is displaced quickly at the staging pressure (an effect similar to a fast-acting valve actuator).

In a shallow seal drum (conventional flashback prevention), the water seals have only a 6-10-in. The sealing-fluid depth in most staging seal drums is typically in the range of 2-5 psig, which is equivalent to 5-12.5 ft of water column. In a deep seal drum, the depth of the sealing fluid is designed to be equal to the staging pressure of the staged flare system. Seal drums serve as a final knockout drum to separate liquid from the relief gases. This prevents air or gas from flowing backward beyond the water seal. The flare gas (or purge gas) is forced to bubble through a layer of water before it reaches the flare stack. Water (or water/glycol mixture) is normally the sealing fluid. Liquid seal drums are vessels that are used to separate the relief gases and the flare/header stack by a layer of liquid. Knockout drums are sized with the gas-capacity equations referred to in Chapter 4 of Volume 1 of the series. PhD, PE, in Surface Production Operations (Third Edition), Vol11.7.4 Seal Drums I know that nobody would have cleaned my dryer the way we did and we had a lot of laughs during the process.Maurice I. I was so happy that we were able to perform this ourselves. When we turned on the dryer it did not make a sound. I order a new wheel and installed it rather quickly since we had learned so much the first time. So, when we had the dryer apart we noticed that there was a lot of black stuff all over and that one of the wheels was not real secure. When we turned the dryer on it squeaked loudly, yikes. It took us about forty-five minutes to put the dryer back together. After installing the new seal we let it dry over night. The part that took the longest was cleaning the old adhesive off the drum. We took the dryer apart in about thirty minutes, after unplugging it.

I just wanted to state that I am a woman and that I performed the repair with my two daughters. I could not find my exact dryer, however, it was close enough for me to get the idea of what to do. I have to admit, I was a little concerned about the installation so again, I looked online for a video. The parts are all numbered so after finding the part, which was easy, all I had to do was scroll down to the number and order. I simply put in the model number of my dryer and the page came up with a picture of my dryer, even the blue color that it is, and several diagrams of all of the parts. Second, I got on Sear Parts Direct to find the seal and was so happy about how easy it was to find the part. First of all, we were getting black marks on our clothes so I found a video online and they suggested that the drum seal may need to be replaced. Wow, ordering and installing the Dryer Drum Seal was easy.
